Taking the pulse of the market
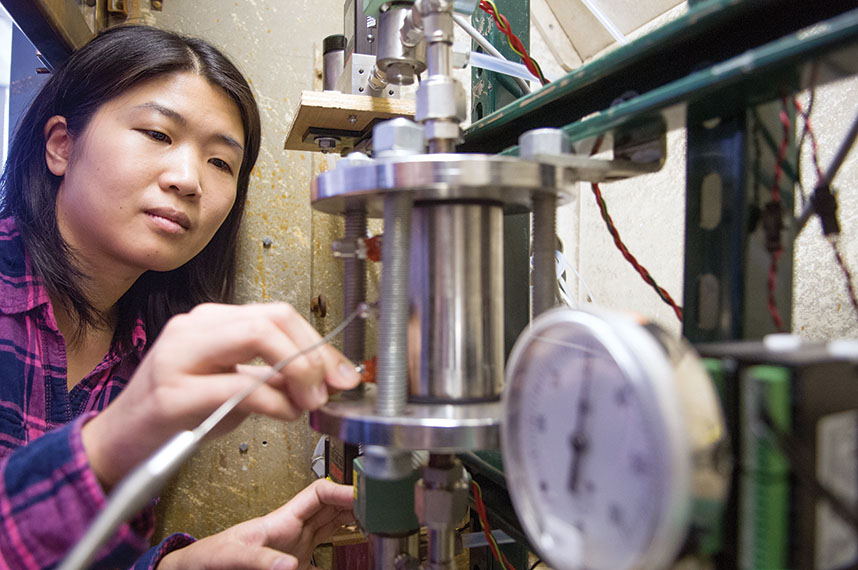
Ph.D. candidate Chin-Wen Wu has helped validate the design of a lighter, smaller and more efficient medical oxygen concentrator for patients with COPD. (Photo by Ryan Hulvat)
If you’ve seen the growing number of TV ads for breathing devices, it won’t surprise you that the National Institutes of Health ranks chronic obstructive pulmonary disease (COPD) as the third-leading cause of death in the United States.
COPD includes a suite of progressive and incurable illnesses, led by emphysema, which reduce the quantity of air flowing into the lungs. This occurs when the tiny airways in the lung lose their elasticity, fill with mucus or become inflamed, or when the walls between airways are destroyed.
To get the oxygen they need, COPD patients were once confined to their beds and connected by breathing tubes to machines filled with compressed oxygen. To leave their homes, they had to carry a cylinder of oxygen or haul a tank on a dolly.
In the past two decades, portable, battery-operated medical oxygen concentrators (MOCs) have enabled many COPD patients to carry on daily activities and even travel.
Mayuresh Kothare, Shivaji Sircar and their students have developed a bench-scale model of an MOC that they believe will significantly exceed the performance of commercial MOCs and improve quality of life for COPD patients.
Kothare, department chair of chemical and biomolecular engineering, and Sircar, adjunct professor in the department, have worked five years on the project. Kothare specializes in constrained and optimal predictive control theory. Sircar, an expert in adsorption science and technology for gas separation, has many years of industrial experience.
The researchers have one patent with a second pending on a technology that would reduce an MOC’s weight while increasing its ability to recover oxygen from the air. They have received funding from the University Science Center in Philadelphia and grants through NSF’s Innovation Corps (I-Corps) and Partnership for Innovation: Accelerating Innovation Research-Technology Translation (PFI:AIR-TT) programs. The support has helped the group learn entrepreneurial skills while building a working prototype.
Smaller, lighter, faster
The bench-scale MOC developed by the Lehigh group improves on current technology in several critical parameters.
Like most commercial MOCs, the Lehigh MOC can be plugged into a wall socket or operated with batteries. It uses a rapid pressure swing adsorption process (RPSA) to generate roughly 90-percent-pure oxygen (O2) from compressed ambient air that contains only about 21 percent O2.
The Lehigh group has reduced device size by employing a single column of adsorbent to separate nitrogen (N2) from O2, as opposed to the two or more columns found in conventional MOCs. This scheme allows the use of a simpler process control system employing fewer switching valves and related hardware. The Lehigh MOC has also demonstrated the ability to produce one to three liters per minute or more of 90-percent-pure O2 from compressed ambient air with process cycle times of three to six seconds. This cycling frequency is three to five times faster than that of commercial portable MOCs.
The Lehigh design uses only a third of the adsorbent inventory (pellets of a type of zeolite, a microporous, aluminosilicate mineral) required by commercial MOCs. This reduces unit weight and size. The design also allows for a continuous rather than a pulsed flow of oxygen, and its size and flow rate can be easily scaled up or down. A “snap on” concept allows the MOC to be hooked to an existing compressed air line for O2 production. This eliminates the need for a dedicated compressor, thus reducing weight while adding to portability. Compressed air lines are available in hospitals, cruise ships and commercial airplanes.
Thus, while current FDA-approved MOCs for ambulatory patients weigh seven to eight pounds and supply about one liter per minute continuously of O2, the Lehigh group hopes to reduce MOC weight to four to five pounds while increasing continuous oxygen supply to two to four liters per minute or more.
And while the batteries in commercial MOCs need recharging after four hours, the goal of the Lehigh group is to increase this duration by about 25 percent.
The group recently reported in AIChE Journal that its results “indicate that the adsorbent inventory of an MOC can be potentially reduced by a factor of three while offering a 10 to 20 percent higher O2 recovery compared to a typical commercial unit.”
A bridge to the market
The I-Corps and PFI:AIR-TT grants have helped the Lehigh group take steps toward commercial deployment of its device. In the I-Corps program, researchers learn the needs of the customer and the market by interviewing consumers. The PFI:AIR-TT grant helps groups develop “proof-of-invention” prototypes. The goal is for researchers to market new products by starting a company or by licensing inventions to existing companies.
Kothare and research scientist Vemula Rama Rao studied supply chain management, marketing and business model canvassing in I-Corps workshops at the University of California at Berkeley. Their textbook was The Startup Owner’s Manual: The Step-By-Step Guide for Building a Great Company by Steve Blank and Bob Dorf. In the course, the researchers refined their ability to explain their technology by making presentations to other research teams, to other I-Corps groups and to Berkeley business faculty members.
Kothare and Rao also interviewed potential consumers of their product, including doctors, patients, medical device and valve manufacturers, and companies that fabricate zeolite. By phone, by Skype and in person, the researchers talked to 100 people. They visited MOC equipment suppliers and hospitals and even went to an oxygen bar in San Francisco where patrons breathe flavored oxygen and chat and watch TV.
The Lehigh group is now building a prototype and talking with potential partners, including medical device companies. Technical hurdles remain. The bench-scale model must be reduced in size to the dimensions of a book. This means smaller valves, compressors and interior hardware. The MOC design, which the group has validated at the bench scale, must now be confirmed at actual commercial size.
The researchers have published 12 papers in journals and conference proceedings. Recently they received a Business Opportunity Validation Grant from the Life Sciences Greenhouse of Central Pennsylvania.
“The commercialization of a new product is a long process,” says Yatin Karpe, associate director of Lehigh’s Office of Technology Transfer. “No one is going to jump on your product because it sounds good—it has to look good, feel good and work well.
“Above all, it has to fit the needs of the customer and the market.”
Posted on: