From biomass to useful products
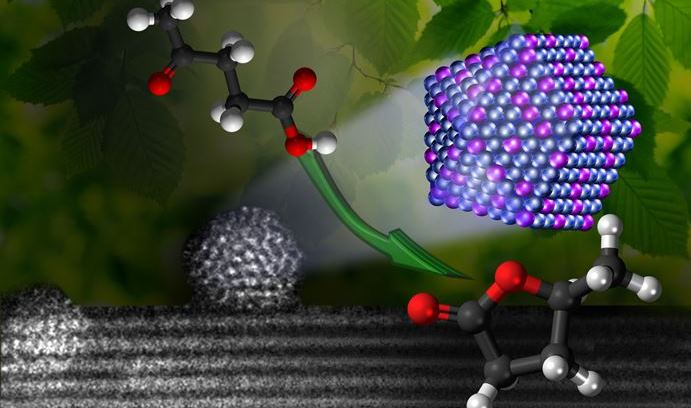
The black-and-white portion of this graphic was generated at Lehigh and shows an electron microscopy image of two Ru-Pd catalyst nanoparticles, measuring 1-2 nm in diameter, on a TiO2 support. The colored portion, computer-generated at Utrecht, shows the conversion of levulinic acid to gamma-valerolactone, a rendition of the Ru-Pd nanoparticle and, in the background, leaves representing renewable biomass.
As scientists seek alternative sources of renewable energy, they are paying increased attention to plants, agricultural residue, household wastes and other forms of biomass.
Wind and solar energy may garner more headlines, but energy experts believe biomass can meet a significant portion of the growing global demand for sustainable materials and fuels.
Critical to this effort are catalysts that can efficiently convert the cellulose in plants into chemical building blocks that in turn are converted into plastics, solvents, fuels and other products.
A group of catalysis experts led by researchers at Utrecht University in The Netherlands has verified the superior performance of a nanoscale alloy catalyst in achieving a key reaction in the processing of biomass into usable products. The group includes researchers from Lehigh and from the UK Catalysis Hub of the Research Complex at Harwell and University College London, both in the United Kingdom.
Using a modified impregnation technique previously published by Christopher J. Kiely, professor of materials science and engineering at Lehigh, the Utrecht researchers fashioned a catalyst consisting of nanoparticles containing the rare metals palladium and ruthenium on a titanium dioxide support.
Using Lehigh’s world-class electron microscopy facilities, Qian He ’12 Ph.D., now with Oak Ridge National Laboratory, imaged and chemically analyzed the Pd-Ru nanoparticles.
The group, which also tested a gold-palladium catalyst on a titanium dioxide support, reported its discovery on March 17 in Nature Communications in an article titled “High Performing and Stable Supported Nano-Alloys for the Catalytic Hydrogenation of Levulinic Acid to γ-Valerolactone.”
“Chemists in Utrecht, together with researchers in the UK and the USA,” the group said in a press release accompanying the article, “have managed not only to speed up a crucial intermediate stage in the processing of biomass, but also to make it more efficient.
“The result of that intermediary stage can subsequently be converted into a variety of valuable renewable products, such as plastics and fuels.”
The benefits of biomass
The advantage of biomass as a renewable energy source is that it can be generated from plants that regrow and have few competing uses. These include switchgrass and other non-edible plants, corn husks and straw, and forest foliage. Lawn clippings, tree trimmings and other household residues, as well as some fast-growing trees, can also generate biomass.
“We currently get a lot of building blocks from petroleum,” says Kiely. “But there’s a finite supply of oil. With biomass, we can regrow it every year. This process of ours takes biomass—wood, leaves and straw and other things that we don’t eat—and converts the cellulose from these into useful chemical building blocks.”
Biomass is composed mostly of cellulose, a fibrous polymeric carbohydrate. During processing, the cellulose is first degraded into levulinic acid (LA), an organic compound. The LA is then hydrogenated into gamma-valerolactone (GVL), a chemical building block that can be converted into fuels, solvents, plastics and even perfumes.
“Many value-added products can in turn be obtained from LA,” the Utrecht group writes in Nature Communications, “including polymer monomers, solvents, plasticizers and fuel components and their precursors. Many of these routes actually involve GVL, a versatile platform molecule in its own right, as intermediate, making the hydrogenation of LA to GVL a reaction of immense importance.”
The Ru-Pd catalyst formulation developed by the Utrecht group converts LA into GVL much more efficiently than the other metal catalysts that have previously been tried for promoting the transformation, says Kiely.
“When engineers design catalysts, they look for three qualities,” says Kiely. “The catalysts should be highly active; that is, they should efficient convert the reactants to products. They should be specific and generate primarily the product that we desire. Finally, they have to be stable so that they can be reused without diminishing their activity and selectivity.
“We have hit all three of these targets. The Ru-Pd catalyst is very active, it very selectively makes GVL, and it’s very durable.
“Other catalysts are being tested for this key reaction but they’re either unstable or they’re inefficient at converting reactants into products. The optimized metal combination—palladium and ruthenium—and the modified impregnation technique make for a stable and efficient catalytic process.”
The modified impregnation technique was developed in 2012 by Meenakshisundaram Sankar and Graham Hutchings Kiely at Cardiff University in the UK in collaboration with Kiely and Qian He at Lehigh. That group described its results in an article in ACS Nano, a journal of the American Chemical Society. Sankar is also a coauthor with Kiely and He on the Nature Communications article.
“When you try to make alloy nanoparticles with conventional methods,” says Kiely, “you usually end up with a wide range of sizes and a spread of chemical compositions in the particles. The modified impregnation technique effectively eliminates these inhomogeneities. It gives you very tight size distribution of ultra-small particles all having a similar composition.”
Aberration-corrected microscopy
After developing the Ru-Pd catalyst and determining its effectiveness at converting LA to GVL, the researchers in Utrecht sent samples to Lehigh, where He used a JEOL JEM-ARM200CF atomic-resolution transmission electron microscope to image and chemically analyze the Ru-Pd nanoparticles.
Acquired two years ago by the Electron Microscopy and Nanofabrication Facility at Lehigh, the JEM-ARM200CF microscope has a third-order-aberration corrector that focuses electrons into an ultra-small probe with a high-current density. Its state-of-the-art Centurio detector collects X-rays emitted from the specimen, allowing spectroscopic chemical analysis at the nanoscale with higher sensitivity and efficiency than any other system.
In addition to scanning transmission electron microscopy, the researchers also used X-ray absorption spectroscopy, X-ray photoelectron spectroscopy and Fourier transform infrared spectroscopy to gain insights into the reason why these bimetallic materials exhibited superior performance in catalyzing the LA-to-GVL conversion.
“The controlled preparation of supported bimetallic nanoparticles via the [modified impregnation] synthesis methodology has a marked, positive effect on the catalysts’ activity, selectivity and stability in the hydrogenation of LA to GVL,” the researchers wrote in Nature Communications.
“On the basis of…detailed characterization, it is found that the beneficial effect of proper Au-Pd and Ru-Pd nano-alloying is the result of electronic modification of Pd in the former catalyst and dilution and isolation of Ru sites in the latter.”
The lead author on the Nature Communications paper is Wenhao Luo, a Ph.D. candidate at Utrecht University. The other authors, in addition to Kiely, He and Sankar, are Pieter C.A. Bruijnincx and Bert M. Weckhuysen of Utrecht University and Andrew M. Beale of University College London.
The Utrecht researchers and Sankar, who developed the new catalyst formulation, have applied for a patent for the use of the Ru-Pd catalyst in the LA-GVL reaction.
Story by Kurt Pfitzer
Posted on: